Project: Knight’s Placard Belt - Jon Fitz John
- sirelesar
- Aug 8, 2023
- 5 min read
Updated: Oct 10, 2023

Photo courtesy of Eva Bogaerts

Figure 1: Venetian velvet plaque belt - with heraldic belt ends, Late 15th Century. (Ref 3 pg21)
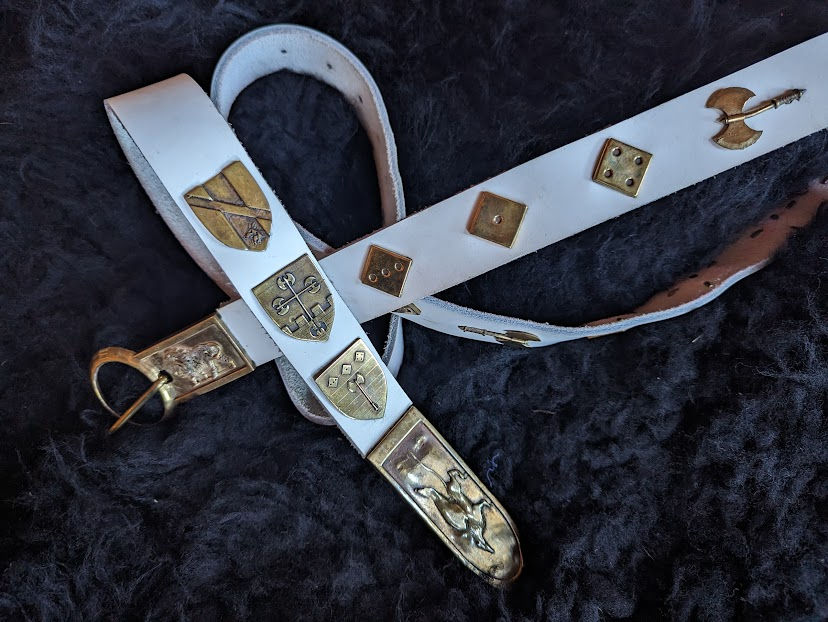


Introduction: Clothing and support belts augmented with heraldic and decorative buckles, tips and symbolism were common throughout the medieval times and antiquity. They were not only instrumental in supporting heavy garments and armor, but they also demonstrated wealth and position by displaying intricate works of art created by the craftsman at the time. They served also to reveal their affiliations and fealties as well as their own personal badges. Above is an example of a late 15th Century girdle demonstrating the use of heraldic shields within the belt. It also demonstrates the use of other badges and symbols throughout the circumference of the girdle, which emblazon the wearer. This project is a plaque belt, made for Jon Fitz John of Drachenwald, formerly my squire in Atlantia. It’s purpose is to commemorate the event of his knighting and serve him in his quest as a knight. The buckle and tip are inspired by extant Norman pieces from the 12th Century, Jon’s persona. They are of a lion on the buckle and a gryphon on the tip. The original pieces were cast for a 1” belt, where I have designed the tip and buckle to accommodate a 1-1/4” belt to accept the lineage shields and preserve their detail. Jon’s device is adjacent to the tip, my device follows, and my knight’s device is atop. The dice and axes around the waist are badges from Jon’s device. My goal for this project was to not only supply Jon with a Knights Girdle, yet to incorporate the varied artifacts and badges around the belt that were employed on the extant pieces. Approach: The period method for creating the metal findings would have varied, based upon the necessity to accommodate the undercut of the piece. Undercut is to cut away material from the underside of an object to leave an overhanging portion in relief. Casting without undercut can be achieved by Sand Casting or other split-block casting technique with the split occurring at the widest part of the original form. Split-block casting also allows the original carving or finding to be recovered, Under-cut castings can only be obtained by the Lost Wax Casting (LWC) approach. The original carving for the LWC must be a material that is able to be melted out of the form with relief, therefore must be a wax, tallow or other material recoverable without maintaining its original form (thus the Lost Wax terminology). As the buckle has an undercut, the original piece was almost certainly performed by LWC. The tip could have been sand or other split-block cast method. I have utilized the LWC process for all of the pieces as multiple reproductions are necessary for this project with the dice and axe badges.
Materials: The intent of use for this belt is for daily wearing of a medieval style belt, made to withstand the rigors of SCA combat, while having low maintenance properties. The materials utilized in creating this piece are intended to provide the look used in period, supply the rigidity for our use while avoiding either the maintenance or cost associated with the period materials.
Element Use | My Materials | Period Materials |
The original unrecoverable model sculpture | Castable Resin (Siraya Tech Cast) | Bees Wax |
The Final Cast Material | Silicon Bronze (95% Cu, 4% Si, 1% Mn) | Bronze (8:1 Cu/Tn Varies) or Gold or Silver. Pewter and Tin were discouraged |
The Duplication Mold - Investment Material | Refractory Ceramic Investment (Prestige Oro) | White, thinned clay |
The belt underneath | White, pre-died leather | Tanned Leather, silk or fine textile. |
Process for Utilizing these Materials: Sculptures: The original lost wax sculpture would have been from bees wax1. Very early forms used tallow. For this project I used a resin specifically for LWC (Siraya Tech Cast) since I was computer modeling and printing the sculptures. The period approach to producing the sculpture would be to carve it by hand, using files, pics and scrapers. I duplicated this process for another project as detailed in Appendix 1 - Model Creation: Wax Carving. For this project, I used a 3D modeling and printing process. The sculptures were created using 3D computer software (XYZMaker 3D Kit, Chitubox) and printed on a 3D resin printer (Elegoo Saturn). I modeled the sculptures for the buckle, tip, all three devices and the dice from basic geometrical components that were manipulated, combined and assimilated. I borrowed the axe shape15, gryphon17 and lion16 from other artists. The sculptures were then 3D printed, as detailed in Appendix 2 - Model Creation: 3D Printing.
Cast Material: The extant pieces would have been gold, silver, or bronze. Bronze is a generic term for a copper-based alloy, with the other constituents being Zinc, Tin, Manganese, Silicon and/or other trace materials. The medieval placard belts utilizing bronze uses mostly copper and tin in varying ratios. The proportions varied widely between 67 and 95% copperX. A common ratio used during the Middle Ages is 1 lb copper to 2 oz tin, which is an 8:1 ratio by weight. This ratio became known as gunmetal in later times. However, the stoichiometric ratio not realized until much later is 9:1, giving the best hardness. I used bronze for this project as gold and silver would be too expensive for reenactment purposes. The bronze metal utilized in the casting includes Copper, Silicon and Manganese, giving the bronze a high sheen with minimal repetitive buffing requirements to maintain the sheen of gold.
Investment: A high-temperature ceramic material is placed around the sculpture, which can withstand the temperatures necessary to burn or melt out the sculpture during the LWC process, and accept the incoming high temperature metal that is the final casting. This is the Investment material. The common investment material during period for LWC was white, thinned clay mixed with dung, then set to age, then strained to create a slurry slip1. This was used for the initial layers of the form. Thicker white clay was then used for subsequent layers of the mold. This slip mold process used for LWC is demonstrated for another project in Appendix 3 – Molding: Slip Molding of a Lost Original. For this project I utilized a refractory ceramic investment (Prestige Oro) to create the mold. This modern ceramic is semi-porous which assists in a vacuum casting process. This vacuum casting process aids in the removal of air around the sculpture while applying the investment, and secondarily aids in drawing the molten cast material into the voids within the investment. Fundamentally, both materials are ceramic, with the latter being engineered for the semi-porous characteristics. The process of applying the modern investment is detailed in Appendix 4 – Molding: Tree Mold for Vacuum Lost Wax and Appendix 5 – Molding: Vacuum Casting an Investment. Backing Belt: The medieval belt would have been either tanned leather, or a silk or other fine textile. I have chosen leather for my project, which has been pre-tanned and dyed white. Although historical knight’s belts are not necessarily white, the SCA uses the white belt as a standard as in some historical traditions knights were dubbed wearing white clothes and a white belt to identify their purity. This does not conclude that all of their belts were white.
Conclusion:
This project assisted me in learning to manage a collage of elements being produced at the same time for a final piece. Many elements were required to be created individually and brought together as a cohesive collection. This is challenging process, of which I will use in future endeavors.
Bibliography:
See Attachment 5 - Bibliography
Kommentare