
Project: Spurs and Buckles
- sirelesar
- Nov 24, 2023
- 4 min read
Updated: Mar 3, 2024
A 12th Century Prick Spur
Introduction:
Spurs are an instrument for aiding a rider in guiding his horse while riding without the use of his hands to steer. This enables the rider to use his hands for other purposes, such as fighting, shooting a bow or other tasks. Spurs have been used for equestrian activities since the La Tene Period in the 5th Century BC by the Celts1. Their original materials were either bone or wood, being tied on with leather or fabric. The yoke, which wraps around the heel, began as a bent piece, was horizontally flat, and did not wrap under the heel bone. Around the early 12th Century, the yoke began to be bent around the heel bone, thus creating an elegant drooping shape. The shank, or the part that protrudes off the back of the heel to prick the horse, began as a simple sharp shaft. Hence, this type of spur is referred to as a Prick spur. The shank was straight out until the 12th Century, where it began to be pointed down away from the yoke to aid the rider who rode straight legged in the saddle. Prick spurs declined in popularity around the early 14th Century after the introduction of the Rowl spur. Around the late 13th, early 14th Century a round pointed star was introduced in place of the single point, which gave rise to the Rowl spur. This enabled the point to be oriented to the horse in multiple riding configurations. The shank of the Rowl spur continued to be pointed down, following the configuration of the transitioning Prick spur, until well into the 17th Century where the shank began to point up.
The buckle, an instrument for terminating and attaching straps of leather began their use in the Roman period and was in a “D” configuration. In the early 12th Century
The spur and the buckle alike were used as a status symbol, with knights having gilded bronze spurs where most others were steel.
This casting project is an attempt to create a 12th Century Prick Spur with the corresponding “D” buckle which would have accompanied them, and a 14th Century Rowl Spur with it’s corresponding buckle system.
Approach:
Material Usage | My Materials | Period Materials |
The original unrecoverable model sculpture | Castable Resin (Siraya Tech Cast) | Bees Wax1 |
The Final Cast Material
| Silicon Bronze (95% Cu, 4% Si, 1% Mn)
| Bronze (4:1 Cu/Tn Varies)1 or Gold or Silver. Pewter and Tin were discouraged. |
The Duplication Mold - Investment Materials | Refractory Ceramic Investment (Prestige Oro) | White, thinned clay (porcelin)1 or gesso (gypsum)2 |
Process for Utilizing these Materials:
Sculptures: The original lost wax sculpture in period would have been made from bees wax1 with very early forms using tallow. The artist would produce the sculpture by carving it by hand, using files, pics and scrapers. On display is an example of an original wax carving for a collar of letters and eagle demonstrating the carving process.
For this project I sculpted the originals with a computer model and created the sculpture on a 3-D printer. The sculptures were modeled using Blender and Chitubox software. I printed the originals using a 3D resin printer (Elegoo Saturn) using a resin specifically for LWC (Siraya Tech Cast). This resin performs like a bees wax and can be completely melted out of the investment mold. Multiple printed originals were placed on a tree to be entombed within an investment form. The originals are melted out of the form, and molten metal formed in their place.
Investment:
The investment is a ceramic material placed around the original sculpture. It can sustain high temperatures without damage when subjected to the LWC burnout process of melting out the wax and when pouring in the molten metal. The common investment material used in period for LWC was white, thinned clay mixed with dung, set to age, then strained to create a slurry slip1. This was used for the initial layers of the mold. Thicker white clay was then used for subsequent layers of the mold. Alternatively, Cellini indicates the use of gesso, or gypsum (2). Fundamentally, these are ceramic refractory materials.
For this project I used a commercially available refractory ceramic investment (Prestige Oro) to create the mold. This ceramic is semi-porous which assists in the vacuum casting process. This vacuum casting process aids in the removal of air around the sculpture while applying the investment, and secondarily aids in drawing the molten cast material into the voids within the investment.
Cast Material:
The extant pieces for collars of this sort would have been gold, silver, or bronze3. Bronze is a generic term for a copper-based alloy, with the other constituents being Zinc, Tin, Manganese, Silicon and/or other trace materials. The medieval collars utilizing bronze used mostly copper and tin in varying ratios. The proportions varied widely between 67 and 95% copper. A common ratio used during the Middle Ages is 4 parts copper to 1 part tin by weight1. This ratio became known as bell metal in later times. However, the stoichiometric ratio not realized until much later is 9:1, giving the best hardness. I used bronze for this project as gold and silver would be too expensive for reenactment purposes. The bronze metal utilized in the casting includes Copper, Silicon and Manganese, giving the bronze a high sheen with minimal repetitive buffing requirements to maintain the sheen of gold.
Conclusion:
This project assisted me in learning about the relationship between the spur development and the parallel development of the buckle.
Bibliography:
1. Bashford Dean, A Descriptive Label for Spurs, The Metropolitan Museum of Art Bulletin, Oct., 1916, Vol.11, No. 10 (Oct., 1916) pp. 217-219 http://www.jstor.com/stable/3253461
2. Hawthore, John G Theophilus – On Divers Arts The Foremost Medieval Treatise on Painting, Glassmaking and Metalwork, Dover Publ., London 1963 ISBN 048623784
3. Ashbee, C.R. – The Treatises of Benvenuto Cellini on Gold Smithing and Sculpture Dover 1967 ISBN 1428604308
4. Gaulker Extant 12th Century Spur https://shop.medievalwares.com/index.php?main_page=product_info&cPath= 65_74_81_83&products_id=1209
Figure 1: The Development of Spurs (1)
Figure 2: A 12th Century Prick Spur

Figure 3: My Replica of the 12th Century Prick Spur

Figure 4: Profile View of the 12th Century Prick Spur

Figure 5: 12th Century Prick Spur showing relative Buckle Design
Figure 6: Extant 14th Century Rowl Spur

Figure 7: My Replica of the 14th Century Rowl Spur
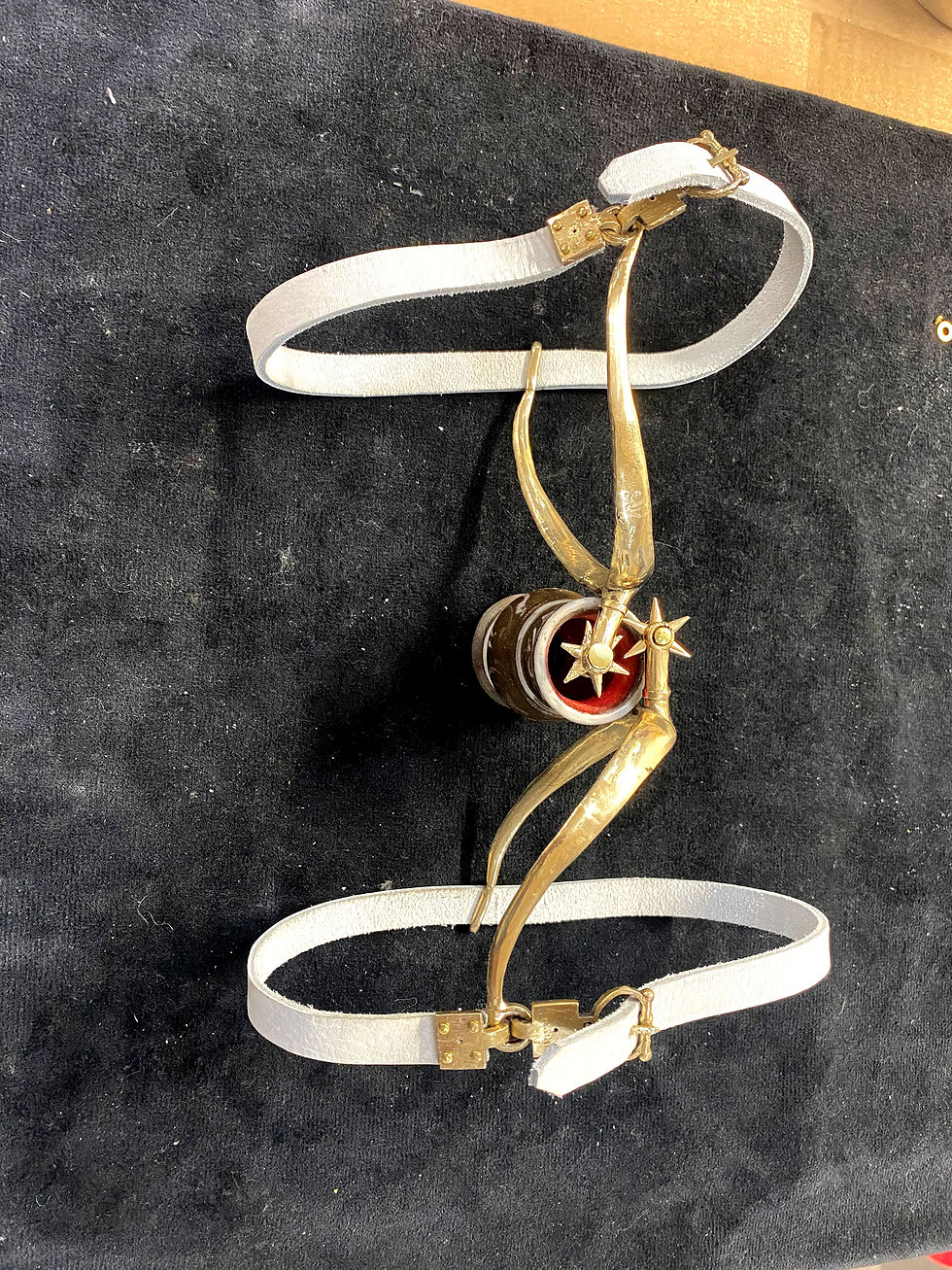
Figure 8: Rowl Spur showing Belt-Buclke interaction
Figure 9: Wax Casting Tree of Spurs and Buckles
Comentarios